Schutzausrüstung und weitere PSA bei ADESATOS kaufen ✆ 0800 8050900
Startseite » Pruefverfahren
Modell 100 | Modell 110 | Modell 200 | Modell 250 | Modell 255 | Modell 310 » Prüfverfahren | Leitfaden | Auswahlhilfe
Prüfverfahren für Schutzanzüge
ChemDefend Schutzanzüge werden strengen Prüfverfahren unterzogen und erst nach Bestehen in den Verkehr gebracht. Grundlage hierfür ist die EN-Verordnung 2016/425. Nachfolgend erhalten Sie Einblick die jeweiligen Testbestandteile.
ABRIEBFESTIGKEIT NACH EN 530: 2010, VERFAHREN 2
Bei dieser Prüfung wird das Martindale-Abriebprüfgerät im umgekehrten Modus verwendet, d. h. der Prüfling wird auf den Abriebtisch gelegt und das Abriebmittel wird in den Probenhalter eingesetzt. Die Prüfung wird an der Außenfläche des Prüfmaterials durchgeführt.
Vier Proben werden auf gewebten Filzkissen montiert und unter einem Prüfkopfdruck von 9kPa mit Schleifgewebe der Körnung 00 für eine vorgegebene Anzahl von Zyklen oder bis zum Versagen abgerieben.
Wenn es nicht möglich ist, die Leistung des Materials mit Hilfe des Druckbehälters zu beurteilen, wie in EN14325 gefordert, wird der Endpunkt durch visuelle Beurteilung gemäß EN 530: 2010 bestimmt.
Der Durchbruch der Probe in einem beschichteten Material ist dann gegeben, wenn die Beschichtungsoberfläche das erste Loch mit einem Durchmesser von mindestens 0,5 mm aufweist, das sich aus dem Verschleiß ergibt (das Loch muss nicht durch das Material hindurchgehen).
Das Material wird wie folgt nach der Anzahl der zur Zerstörung der Barriereschicht erforderlichen Abrasionszyklen klassifiziert, wobei das niedrigste Einzelergebnis aus den 4 Messungen genommen wird.
- Klasse 1 > 10 Zyklen
- Klasse 2 > 100 Zyklen
- Klasse 3 > 500 Zyklen
- Klasse 4 > 1000 Zyklen
- Klasse 5 > 1500 Zyklen
- Klasse 6 > 2000 Zyklen
BESCHÄDIGUNG DURCH BIEGEN NACH EN ISO 7854 1997, VERFAHREN B
Drei Proben werden in Lauf- und Querrichtung (MD und CD) für eine vorgegebene Anzahl von Zyklen oder bis zur Erkennung von Schäden an der Außenfläche des Prüfmaterials geprüft.
Wenn es nicht möglich ist, die Leistung des Materials mit Hilfe des Druckbehälters zu beurteilen, wie in EN14325 gefordert, wird der Endpunkt durch visuelle Beurteilung bestimmt. Als Endpunkt gilt, wenn sich in der bis zur Basisschicht reichenden Barriereschicht ein Riss gebildet hat.
Das Material wird nach der Anzahl der Zyklen klassifiziert, die zur Rissbildung an der Schutzschicht erforderlich sind, und zwar mit der niedrigsten Einzelzahl aus den 6 gemessenen Prüfergebnissen.
- Klasse 1 > 1000 Zyklen
- Klasse 2 > 2500 Zyklen
- Klasse 3 > 5000 Zyklen
- Klasse 4 > 15000 Zyklen
- Klasse 5 > 40000 Zyklen
- Klasse 6 > 100000 Zyklen
WEITERREISSFESTIGKEIT NACH EN ISO 9073-4: 1997.
Fünf Proben werden in Lauf- und Querrichtung (MD und CD) vorbereitet und wie in der Norm beschrieben konditioniert. Es wird eine Kraft aufgebracht, um einen Schnitt im Prüfling stetig zu verlängern. Die mittlere maximale Reißfestigkeit wird in Newton angegeben.
Die Leistung des Materials wird anhand des mittleren Ergebnisses für die 5 gemessenen Werte in sowohl MD als auch CD des Materials klassifiziert.
- Klasse 1 > 10 N
- Klasse 2 > 20 N
- Klasse 3 > 40 N
- Klasse 4 > 60 N
- Klasse 5 > 100 N
- Klasse 6 > 150 N
ZUGEIGENSCHAFTEN NACH DIN EN ISO 13934-1: 1999
In jeder Richtung werden fünf Proben vorbereitet, jede 50 mm breit und mit ausreichender Länge für die Verwendung einer Messlänge von 200 mm. Die Prüfungen werden auf einer CRE-Zugprüfmaschine von Testometric durchgeführt, ausgestattet mit flachen Backen, die mit einer Auszugsgeschwindigkeit von 100 mm pro Minute arbeiten. Es wird eine Vorspannung von 2 Newton angewandt.
Die Leistung des Materials wird anhand des mittleren Ergebnisses für die 5 gemessenen Werte in sowohl MD als auch CD des Materials klassifiziert.
- Klasse 1 > 30 N
- Klasse 2 > 60 N
- Klasse 3 > 100 N
- Klasse 4 > 250 N
- Klasse 5 > 500 N
- Klasse 6 > 1000 N
WIDERSTAND GEGEN DURCHSTOSSEN NACH EN 863: 1995
Vier Materialproben werden mit der Außenfläche zur Prüfsonde getestet. Die maximale Kraft, die erforderlich ist, um den Dorn durch die Probe zu drücken, wird als Durchstoßfestigkeit erfasst. Der Mittelwert wird auf die nächste ganze Zahl gerundet und die Leistung des Materials anhand des mittleren Ergebnisses der 4 Messungen nach den folgenden Leistungsstufen klassifiziert:
- Klasse 1 > 5 N
- Klasse 2 > 10 N
- Klasse 3 > 50 N
- Klasse 4 > 100 N
- Klasse 5 > 150 N
- Klasse 6 > 250 N
Quelle: https://chemdefend.co
BLOCKWIDERSTAND UND HITZEBESTÄNDIGKEIT NACH ISO 25978:1990
Die Prüflinge werden paarweise, Rückseite an Rückseite, Vorderseite an Vorderseite und Vorderseite an Rückseite zwischen zwei Glasscheiben angeordnet und anschließend in einem Ofen 3 Stunden lang einer Temperatur von 70+/- 2 °C unter einer Masse von 5,0 kg ausgesetzt.
Nach einer Stunde Abkühlung werden die Proben getrennt und auf Haftung oder Ablösung der Beschichtungen untersucht. Die Probe wird nach der schlechtesten Bewertung klassifiziert.
Kein Blocken – die beschichteten Oberflächen trennen sich ohne Anzeichen von Verklebung.
Leichtes Blocken – eine gewisse Haftung der beschichteten Oberflächen erfolgt bei der Trennung, jedoch ohne Beschädigung der Beschichtung.
Blocken – die beschichteten Oberflächen sind schwer zu trennen; die Beschichtung oder ein Teil der Beschichtung wird bei der Trennung abgelöst.
Penetrationswiderstand gegen WASSER NACH DIN EN 20811: 1992 (1996) (ISO 811: 1981)
Textilien – Bestimmung des Penetrationswiderstandes gegen Wasser – Hydrostatische Druckprüfung.
Die vom Material getragene hydrostatische Förderhöhe ist ein Maß für den Widerstand gegen den Wasserdurchtritt durch das Material. Eine Probe von 100 cm² (113 mm Durchmesser) wird einem Wasserdruck ausgesetzt, der von unten auf die Oberfläche der Probe aufgebracht wird, mit einer Steigerungsrate von 60 ± 0,5 cm pro Minute und einer Temperatur von 20 +/- 2 C. Der Druck, bei dem das Wasser an der dritten Stelle eindringt („3. Tropfenbildung“), wird notiert. Fünf Proben werden getestet und der Mittelwert bestimmt.
EN1149-5:2008
Bestimmung des Oberflächenwiderstandes nach EN1149-1:2006
Die Probe wird konditioniert und bei 23 ± 1°C und 25 ± 5 % relativer Luftfeuchtigkeit getestet.
Der Oberflächenwiderstand der Probe wird nach dem in EN 1149-1:2006 festgelegten Verfahren bestimmt.
Eine Oberfläche muss einen Oberflächenwiderstand von ≤ 2.5 x 109 Ohm aufweisen.
Bestimmung des Ladungsabbaus nach EN1149-3:2004
Die Probe wird konditioniert und bei 23 ± 1°C und 25 ± 5 % relativer Luftfeuchtigkeit getestet.
Die Ladungsabbauzeit und die Abschirmwirkung werden nach DIN EN 1149-3: 2004 Verfahren 2 Induktionsladung gemessen und ein Wert von weniger als 4 Sekunden für die halbe Abbauzeit und/oder den Abschirmfaktor von > 0,2 ist aufzuzeichnen.
Quelle: https://chemdefend.co
Typ | Standard & Testmethode | Testbeschreibung | |
---|---|---|---|
Typ 3 Spritzstrahltest | EN 14605+A1 :2009 EN ISO 17491-3 :2008 | ![]() | Der ganze Overall wird einer Reihe von kurzen, direkten Strahlen einer wasserbasierten Flüssigkeit (mit geringer Oberflächenspannung von 30-35 m N/m) ausgesetzt. Die Strahl- düsen sind in 1 m Entfernung vom Overall platziert und der Abgabedruck beträgt 3 bar. Die Flüssigkeit ist gefärbt, so dass eine Leckage die Unterkleidung sichtbar verfärbt. Die Prüfung gilt als bestanden, wenn die gesamte verfärbte Fläche auf der Unterklei- dung kleiner als das Dreifache des Kalibrierflecks ist. (Der Kalibrierfleck ist die Fleckenfläche, die durch 0,02 ml der Prüfflüssigkeit entsteht.) |
Typ 4 Sättigungs- Sprühtest | EN 14605+A1 :2009 EN ISO 17491-4 :2008, Methode B | ![]() | Bei dieser Prüfung wird der ganze Overall einem Sprühnebel aus einer wasserbasierten Flüssigkeit (mit einer geringen Oberflächenspannung von 30-35 m N/m) ausgesetzt. Eine Gesamtmenge von 4,5 L wird für 1 Minute als feiner Nebel versprüht. Eine direkte Bestrahlung des Overalls erfolgt nicht. Während des Sprühens führt die Testperson ein definiertes, sanftes Bewegungsprogramm aus und dreht sich dabei. Die Flüssigkeit ist gefärbt, so dass eine Leckage die Unterkleidung sichtbar verfärbt. Die Prüfung gilt als bestanden, wenn die gesamte verfärbte Fläche auf der Unterklei- dung kleiner als das Dreifache des Kalibrierflecks ist. (Der Kalibrierfleck ist die Fleckenfläche, die durch 0,02 ml der Prüfflüssigkeit entsteht.) |
Typ 5 Leckage von Partikeln Nach innen | EN ISO13982-1:2004+A1:2010 EN ISO 13982-2 Methode B | Bei dieser Prüfung wird ein ganzer Overall (10 Prüfanzüge) einem trockenen Natriumchlorid-Aerosol (Partikelgröße = 0,6 μm) ausgesetzt. Währenddessen führt die Testperson folgende Sequenz von 3 Bewegungen durch: 9 Minuten stehen, 9 Minuten gehen, 9 Minuten hocken. Die Gesamt-Eintrittsleckage wird als Prozentsatz der Natrium- chloridkonzentration außerhalb des Anzuges ausgedrückt. Jede Anzug wird an 3 Punkten – Knie, Taille und Brust – gemessen. Für jeden Overall werden somit 9 Messungen ausgeführt. Eine Prüfung gilt als bestanden, wenn die Eintrittsleckage bei 82 von 90 Messungen weniger als 30 % beträgt. (Ljmn, 82/90 ≤ 30 %). Außerdem muss die durchschnittliche Eintrittsleckage (aus allen Bewegungen und Messpositionen) bei 8 von 10 Overalls weniger als 15 % betragen. (Ls, 8/10 ≤ 15%). | |
Typ 6 Niedrigniveau-Spritztest | EN 13034 :2005+A1 :2009 EN ISO 17491-4 :2008 Method A | ![]() | Diese entspricht der Typ 4 – Prüfung, jedoch ist die vernebelte Flüssig- keitsmenge auf 1,9 L reduziert und die Oberflächenspannung auf 57 m N/m erhöht. Die Prüfung gilt als bestanden, wenn die gesamte verfärbte Fläche auf der Unterkleidung kleiner als das Dreifache des Kalibrierflecks ist. (Der Kalibrierfleck ist die Fleckenfläche, die durch 0,02 ml der Prüfflüssigkeit entsteht.) |
Quelle: https://chemdefend.co
PENETRATION
Ein physikalischer Prozess, bei dem eine Flüssigkeit ein textiles Material durchdringt, indem sie durch Poren oder Löcher hindurchgeht.
ABWEISUNG
Beschreibt die Eigenschaft eines textilen Materials, eine Flüssigkeit nicht zu absorbieren.
EN 6530: RINNENTEST
- Das Textilmaterial wird in eine geneigte Rinne (45°) gelegt, die mit einem absorbierenden Material ausgekleidet ist.
- 10 ml der Testflüssigkeit werden innerhalb von 10 Sekunden am oberen Ende auf das Testgewebe gegossen.
- Die Flüssigkeitsmenge, die innerhalb von 1 Minute das Gewebe durchdringt und vom Untermaterial absorbiert wird, wird als Prozentsatz der Ursprungsmenge ausgedrückt („Penetrationsindex“)
- Die Flüssigkeitsmenge, die innerhalb 1 Minute vom Becherglas aufgefangen wird, wird ebenfalls als Prozentsatz der Ursprungsmenge ausgedrückt („Abstoßungsindex“).
- Gemäß der europäischen Norm EN 6530 wird sowohl die Flüssigkeitspenetration als auch die Flüssigkeitsabweisung durch ein Material gemessen.
- Die Penetrationsergebnisse für jede Chemikalie werden in 3 Leistungsklassen eingeteilt:
Leistungsklasse | Abweisungsindex | Penetrationsindex |
---|---|---|
Nicht klassifiziert | < 80% | > 10% |
Klasse 1 | > 80% | < 10% |
Klasse 2 | > 90% | < 5% |
Klasse 3 | > 95% | < 1% |
- Der Absorptionsindex bezieht sich auf den Prozentsatz der im Prüfmaterial enthaltenen, aber nicht durchgedrungenen Prüfflüssigkeit.
PRÜFCHEMIKALIEN
- 30%ige Schwefelsäure
- 10%iges Natriumhydroxid
- Xylol
- Butan-1-ol
Hinweis:
Der Penetrationsindex nach EN 6530 kann nur als Hinweis auf die sofortige Penetration bei kleinen Mengen flüssiger Chemikalien verwendet werden.
Wird das Material länger als 1 Minute größeren Mengen ausgesetzt, können erhebliche Mengen durchdringen.
Quelle: https://chemdefend.co
WAS IST PERMEATION?
Permeation ist ein Prozess, bei dem eine feste, flüssige oder gasförmige Chemikalie ein Material auf molekularer Ebene durchdringt. Die Permeation kann durch das folgende vereinfachte Diagramm dargestellt werden.
- Absorption von Molekülen an der (äußeren) Oberfläche des Materials.
- Diffusion der Moleküle durch das Material.
- Desorption der Moleküle an der gegenüberliegenden (inneren) Oberfläche des Materials.
PERMEATIONSMESSUNG
Die Barriereeigenschaften eines Materials oder einer Naht gegenüber der Permeation durch eine potenziell gefährliche Chemikalie werden durch Messung der Durchbruchzeit und der Permeationsrate durch das Material bestimmt. Permeationstests werden nach den Prüfmethoden ASTM F739, EN 369 oder EN 374-3 durchgeführt. Die Wahl der Methode ist abhängig von der Art des Gefahrstoffs sowie nationalen und örtlichen Vorschriften.
Die Außenfläche des Barrierematerials wird in einer Permeationsprüfzelle dem Gefahrstoff (flüssige oder gasförmige Chemikalie) ausgesetzt. Der Durchgang der Chemikalie wird durch Probenahme auf der Innenseite (Sammelseite der Zelle) und massenspektroskopischer Detektion überwacht.
Permeationsrate (PR)
Die Permeationsrate ist die Geschwindigkeit, mit der eine Chemikalie durch das Barrierematerial hindurchtritt. Die Permeationsrate wird ausgedrückt als die Masse der Chemikalien, die pro Zeiteinheit durch das Barriereaterial hindurchtritt, z. B. 2,0 µg/cm2/min bzw. 2 Millionstel eines g pro Quadratzentimeter pro Minute.
Permeationsrate im stationären Zustand (SSPR)
Die „Steady-State“-Permeationsrate, stellt sich nach dem Durchbruch ein, und zwar dann, wenn alle, die Permeattionsrate beeinflussenden Faktoren im Gleichgewicht stehen.
Minimal detektierbare Permeationsrate (MDPR)
Die minimal detektierbare Permeationsrate ist eine Funktion der Messempfindlichkeit der Analyseeinheit, des Messraumvolumes und der Messdauer. Die minimale nachweisbare Permeationsrate kann in bestimmten Fällen nur 0,001 μg/cm2 pro Minute betragen.
TATSÄCHLICHE DURCHBRUCHZEIT ODER „BREAKTHROUGH-DETECTION-TIME“ (BDT)
Die durchschnittliche Zeit zwischen dem ersten Chemikalienkontakt mit der Materialaußenfläche und dem ersten Nachweis der Chemikalie an der Innenfläche.
Eine tatsächliche Durchbruchzeit von > 480 Minuten und eine Permeationsrate von „nd“ (not detected, nicht erkannt) bedeutet nicht, dass keinerlei Permeation erfolgt ist. Es bedeutet jedoch, dass die Permeationsrate auch nach einer Messzeit von acht Stunden unterhalb der minimalen Nachweisgrenze (MDPR) des Analysegerätes liegt.
Bei der Auswahl eines Barrierematerials gegen eine bestimmte Chemikalie werden MDPR und (erwartete) Expositionszeit verwendet, um zu bestimmen, ob – unter Berücksichtigung der Toxizität der Chemikalie – die Schutzleistung ist.
NORMALISIERTE DURCHBRUCHZEIT – NACH ASTM F739
Die durchschnittliche verstrichene Zeit zwischen dem ersten Kontakt der Chemikalie mit der Außenfläche des Materials und dem Zeitpunkt, zu dem die Chemikalie an der Innenfläche des Materials mit einer Permeationsrate von 0,1 μg/cm2/min nachgewiesen wird.
NORMALISIERTE DURCHBRUCHZEIT – NACH EN 374-3
Die durchschnittliche verstrichene Zeit zwischen dem ersten Kontakt der Chemikalie mit der Außenfläche des Materials und dem Zeitpunkt, zu dem die Chemikalie an der Innenfläche des Materials mit einer Permeationsrate von 1,0 μg/cm2/min erfasst wird. Somit ist die Durchbruchzeit „normalisiert“, da sie unabhängig von der Empfindlichkeit des Analysators ist. Hier wird der niedrigste Wert der Durchbruchzeit erfasst.
Eine normalisierte Durchbruchzeit von > 480 Minuten bedeutet, dass die durchschnittliche Permeationsrate nie die definierte Rate von 1,0 μg/cm² /min erreicht hat. Allerdings kann ein Durchbruch der Chemikalie tatsächlich stattgefunden haben, aber mit einer niedrigeren Rate.
LEISTUNGSKLASSIFIZIERUNG VON NORMALISIERTEN DURCHBRUCHZEITEN
Nach den europäischen Normen für Chemikalienschutzkleidung muss die Beständigkeit von Bekleidungsmaterialien gegen Permeation durch Chemikalien nach EN 369 oder EN 374-3 gemessen werden. Die normalisierten Durchbruchzeiten werden in sechs Leistungsklassen eingeteilt. Für die Europäische Norm ist die Korrelationstabelle zwischen der normalisierten Durchbruchzeit in Minuten und der Leistungsklasse in der folgenden Tabelle dargestellt
Durchbruchzeit (EN 369) in Minuten | EN-Klasse |
---|---|
>= 10 | Klasse 1 |
>= 30 | Klasse 2 |
>= 60 | Klasse 3 |
>= 120 | Klasse 4 |
>= 240 | Klasse 5 |
>= 480 | Klasse 6 |
Quelle: https://chemdefend.co
Nach der EU-Richtlinie 2000/54/EG über biologische Stoffe sind Arbeitgeber verpflichtet, ihren Arbeitnehmern geeignete Schutzkleidung zur Verfügung zu stellen. Zum Schutz vor Bakterien, Viren und anderen Mikroorganismen werden nach EN 14126 spezifische Anforderungen an die Bekleidungsmaterialien zum Schutz vor Infektionserregern definiert. Diese Materialien müssen die Haut und damit den Träger vor dem möglichen Kontakt mit biologischen Stoffen schützen und die Ausbreitung von Keimen verhindern. Anzüge mit versiegelten Nähten werden empfohlen, da Viren, Bakterien und Sporen klein genug sind, um durch die Öffnungen der Nähte zu dringen.
SCHUTZKLEIDUNGSTYPEN NACH EN 14126:2003
Typbeschreibung und relevante Norm
- 1aB, 1bB, 1cB, 2B gasdicht, nicht gasdicht EN 943-1
- EN 14605 3B Schutz gegen druckbeaufschlagte flüssige Chemikalien
- EN 14605 4B Schutz gegen Flüssigkeitssättigung
- EN 13034 6B Begrenzter Schutz gegen Flüssigkeitsnebel oder -spritzer
- EN ISO 13982-1 5B Schutz gegen luftgetragene Feststoffpartikel
EN 14126 UMFASST DIE FOLGENDEN MATERIALPRÜFUNGEN:
- Penetrationsprüfung mit synthetischem Blut (ISO/FDIS 16603)
- Penetrationswiderstand gegen Viren (ISO/FDIS 16604)
- Penetrationswiderstand gegen Bakterien (ISO/DIS 22610)
- Penetrationswiderstand gegen biologisch verunreinigte Aerosole (ISO/DIS 22611)
- Penetrationswiderstand gegen kontaminierten Staub (ISO/DIS 22612)
VORPRÜFUNG NACH ISO/FDIS 16603
Dies ist ein visueller Screening-Test, um festzustellen, bei welchem Prüfdruck die Viruskulturprüfung durchgeführt werden soll. Für diese Prüfung wird eine synthetische Blutmischung aus Cellulose, Farbstoff, Pufferlösung und Stabilisierungsmitteln verwendet. Es wird der Druck gemessen, bei dem die Flüssigkeit durch das Material dringt.
VIRUSKULTURPRÜFUNG NACH ISO/FDIS 16604: UNTER VERWENDUNG DES IN ISO 16603 FESTGELEGTEN GRENZWERTES
Der aus ISO 16603 bestimmte Penetrationsdruck in kPa wird als Expositionsdruck für diese Prüfung verwendet, mit bestandener Prüfung, mit Klassifizierung oder fehlerhaftem Ergebnis. Die Virusprüfung folgt ähnlichen Protokollen wie ISO/FDIS 16603, wobei der Hauptunterschied darin besteht, dass anstelle von synthetischem Blut eine mit einem Bakteriophagen oder Virus (Phi-X-174) verunreinigte Flüssigkeit verwendet wird. Jede Penetration durch das Prüfmaterial wird durch Kultivieren von Verunreinigungen auf einer Agarplatte erkannt.
Klassifizierung nach ISO 16604
Klasse | Expositionsdruck [kPa] |
---|---|
6 | 20.0 |
5 | 14.0 |
4 | 7.0 |
3 | 3.5 |
2 | 1.75 |
1 | 0.0 |
BAKTERIENPRÜFUNG NACH ISO/DIS 22610:
Die Norm definiert das Verfahren zur Prüfung des Penetrationswiderstands eines Materials gegen nasse Bakterien. Beim Prüfverfahren wird das bakteriell verunreinigte (Staphylococcus Aureus) Spendermaterial auf 10 Mikron HDPE auf das zu prüfende Barrierematerial aufgebracht, auf eine Agarplatte gelegt und mechanisch gerieben. Jede Penetration durch das Material wird kultiviert und auf einer Agarplatte gegen eine Kontrolle gemessen. Es gibt sechs Klassen, wie in der Norm definiert, mit den entsprechenden Durchbruchzeiten, die den Punkt angeben, an dem die Bakterien das Barrierematerial messbar durchdringen.
Klassifizierung nach ISO/CD 22610 – Penetrationswiderstand gegen Bakterien
Klasse | Bakterienpenetration [min] |
---|---|
6 | > 75 |
5 | > 60 |
4 | > 45 |
3 | > 30 |
2 | > 15 |
1 | < 15 |
AEROSOLPRÜFUNG NACH ISO/DIS 22611:
Die Barrierewirkung des Prüfmaterials gegenüber biologisch kontaminierten Aerosolen wird mit einer Bakterienlösung von Staphylococcus Aureus gemessen, die in einem Aerosol suspendiert und sowohl auf eine ungeschützte Cellulose-Nitrat-Membran als auch auf eine mit dem zu prüfenden Barrierematerial bedeckte Membran gesprüht wird (die Porengröße der Membran beträgt ca. 0,45 μm). Die Prüfung findet in einer geschlossenen Kammer statt. Beide Membranen werden anschließend analysiert, um ihre bakterielle Belastung durch Kultivierung auf einer Agarplatte festzustellen. Zur Klassifizierung der Ergebnisse wird das Penetrationsverhältnis (Verhältnis der Belastung der ungeschützten Cellulose-Nitrat-Membran zur Belastung der mit dem Prüfmaterial geschützten Membran) berechnet und in Log-Einheiten dargestellt
Klassifizierung nach ISO/DIS 22611 – Penetrationswiderstand gegen biologisch kontaminierte Aerosole
Klasse | Penetrationsrate ohne/mit Prüfmaterial [log] |
---|---|
3 | > 5 |
2 | > 2 |
1 | > 1 |
STAUBPRÜFUNG NACH ISO/DIS 22612:
Um die Barriere gegen kontaminierten Staub zu messen, werden die Prüfmaterialien vorsterilisiert und dann in der Prüfvorrichtung fixiert und mit kontaminiertem (Bacillus Subtilis) Talkumpuder dosiert. Darunter befindet sich eine Agarkulturplatte. Die Prüfvorrichtung wird bewegt oder geschüttelt. Die das Material durchdringenden Partikel werden kultiviert und nach Inkubation der Agarplatte gezählt, und ein nicht kontaminierter Prüfling wird als Kontrolle durchgeführt. Die Ergebnisse (Mittelwerte aus 10 Einzelergebnissen zu einem bestimmten Zeitpunkt) werden in Penetrations-Log-Einheiten gemessen
Klassifizierung nach ISO/DIS 22612 – Widerstand gegen kontaminierten Staub (CFU: Colony Forming Units, koloniebildende Einheiten)
Klasse | Penetrationsrate mit/ohne Prüfmaterial [log] |
---|---|
3 | ≤ 1 |
2 | ≤ 2 |
1 | ≤ 3 |
Quelle: https://chemdefend.co
Teil 2 – Anforderungen an unbelüftete Schutzkleidung gegen radioaktive Kontamination durch feste Partikel.
Als Prüfverfahren wird das in EN ISO 13982-2 Verfahren B definierte Gesamtleckageverfahren nach innen verwendet.
Die Prüfung folgt im Wesentlichen den gleichen Protokollen wie die Prüfung Typ 5.
Bei dieser Prüfung wird ein ganzer Anzug (6 Prüfanzüge oder mehr) einem trockenen Aerosol von Natriumchlorid ausgesetzt. Die Partikelgröße ist 0,6 μm. Während er dem trockenen Aerosol ausgesetzt ist, führt der Träger des Anzugs die folgende Sequenz von Bewegungen durch: stehen, gehen, hocken Die gesamte Leckage nach innen wird als Prozentsatz der Natriumchloridkonzentration außerhalb des Anzuges ausgedrückt, die für jeden Prüfanzug an 3 Punkten – Knie, Taille und Brust – gemessen wird. Daher werden für jeden Anzug 9 Messungen durchgeführt und die 54 Ergebnisse wie folgt gemittelt und konsolidiert:
Position | Knie | Taille | Brust | Durchschnitt |
---|---|---|---|---|
Stehen | TILE % | |||
Gehen | TILE % | |||
Hocken | TILE % | |||
Durchschnitt | TILA % |
Aus den Durchschnittswerten werden dann folgende Werte ermittelt:
Gesamte Leckage nach innen % – TILA % – durchschnittliche Ergebnisse aller 6 Träger, aller Aktivitäten und aller Positionen.
Gesamte Leckage nach innen % -TILE % – durchschnittliche Ergebnisse der Leckage nach innen aller 6 Träger, aller Positionen für eine Aktivität beim Stehen, Gehen oder Hocken.
Der höchste Mittelwert der gesamten Leckage nach innen für eine Aktivität – der höchste TILE % und der TILA % – werden dann zur Bestimmung des nominalen Schutzfaktors gemäß der folgenden Tabelle verwendet..
Unbelüftete Schutzkleidung ist nach DIN EN 1073-2:2002 zu klassifizieren.
Klasse | Mittelwert der Leckage nach innen der drei Probestellen im Inneren des Anzugs beim Stehen, Gehen oder Hocken – 6 Anzüge: 9 Messungen pro Anzug aufgezeichnet. | Nominaler Schutzfaktor | |
---|---|---|---|
Eine Aktivität TILE % | Alle Aktivitäten TILA % | ||
3 | < 0.3 | < 0.2 | 500 |
2 | < 3.0 | < 2.0 | 50 |
1 | < 30.0 | < 20.0 | 5 |
Quelle: https://chemdefend.co
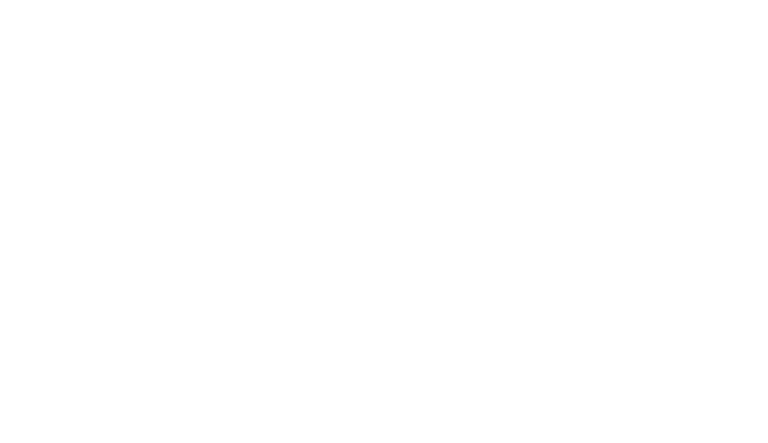
ADESATOS bietet Desinfektionslösungen durch Kaltvernebelung für Altenheim, Pflegeheim, Krankenhaus, Rettungsdienst, Pharma und
viele weitere Bereiche. Sprechen Sie uns an. Unsere Desinfektionsmittel aus Wasserstoffperoxid (H2O2) mit Silberionen entfernt Erreger bei der Raumdesinfektion oder Fahrzeugdesinfektion
Anbieter
- ADESATOS GmbH
- Reichardsweide 46
- DE-63654 Büdingen
- T: +49 (0)6042 9781680
- F: +49 (0)6042 9781680
- E: info@adesatos.com
- I: adesatos.com